Continuing the discussion of data driven standards and the gaps in data that all companies have to deal with, this blog will address the problems of missing work flow data and missing metrics.
Missing Work Flow Data
A normal warehouse management system (WMS) will only capture about 50-60% of the actual work flow that occurs in any operation. Your time clock will show an employee at work for 8 hours, but you may only see 5 hours, or even fewer, of active time on your WMS. That is a lot of money you are spending without having any idea of where it’s actually going. From our experience, that work flow time is untracked time that is either direct labor not being captured, indirect labor not being captured, or missing time (you have no idea). A common example of this is unloading/receiving, a direct labor process not normally captured by the WMS (usually the first capture point of the work flow is at staging or putaway). Other examples of untracked time include indirect processes such as morning all-hands meetings, battery changes, and cleaning.
To account for this time accurately, you need a job coding system. Newer WMS software gives you the ability to track indirect processes. There are also several job coding systems available. Easy Metrics comes with a product called Job Trak , which makes it easy for employees to track both indirect labor and non-WMS direct labor and metrics.
Incorporating a job coding system requires proactive change management to make sure employees are properly tracking their non-WMS work flow. The end goal is for you to know where every minute of the day is being spent and then allocate it to a cost center. Once all work flow is tracked properly, you can then work to improve employee utilization and effectiveness. Conceptually, the goal would be to have the level of visibility illustrated below:
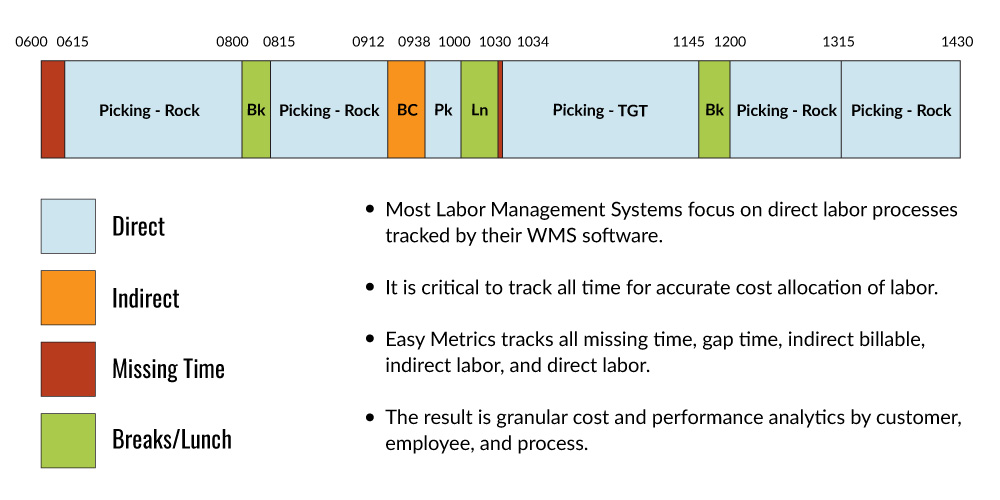
Missing Metrics
Missing metric data is a bit more complicated to address. When developing labor standards, you need metrics that help you develop the standard. For example, for the process picking you may have metrics such as lines, locations, distance, cube, weight, cases, eaches, and/or pallets, all of which could be used to develop the standard. However, in the actual WMS scan data, you may only have units, UOM, and lines. When building the labor standard of the reduced metric set, if the standard deviation of the labor standard is excessive, then it means you likely need additional metrics to build a more consistent standard. To get these extra metrics, you will need to modify your WMS system to enable you to get that additional information. You may also need to bring in other data sets.
This is a far more involved process with regards to both cost investment and time. For processes that have a high standard deviation on performance, we usually recommend working with an Industrial Engineer to determine what additional metrics will help you better build the labor standard. You would then work with your IT department to configure your WMS to get that metric data. Metrics like travel time and distance are derived from the location data and facility mapping, and they will require a labor management system to calculate.
The above may sound onerous, but it normally only affects a small percentage of processes. The majority of process labor standards can be calculated from the WMS data sets. From an ROI perspective, it is definitely worth the effort to ensure that any gaps in your data are filled in. Since labor is about 70% of the cost in a distribution center, small improvements in labor efficiencies and utilization can have a profound impact on your bottom line.